
Raising the board on high-performance gypsum products
In part one of a three-blog series, learn what drives the culture of innovation at National Gypsum
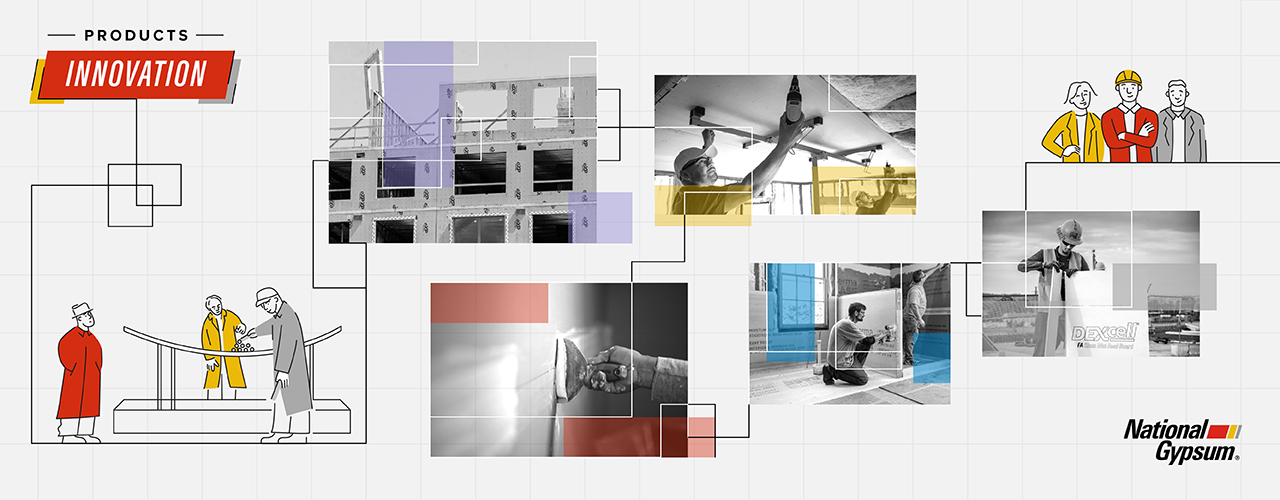
When gypsum board replaced wood and gypsum lath and plaster in the early 20th century as the primary construction material for interior walls, it represented a big leap forward in construction technology. Gypsum board not only sped up construction and lowered costs but also added the functional benefits of fire and sound resistance.
When founded in 1925 in Buffalo, New York, National Gypsum developed and manufactured a new and advanced gypsum board designed to perform better and simplify installation. Nearly a century later, the National Gypsum family of companies continues to incorporate fresh, innovative performance features into gypsum wallboard. Whether it’s adding mold, mildew and moisture resistance, making the boards lighter and easier to handle, or developing panels that stand up to severe impact, innovating to create high-performance building products has been part of the company’s DNA since the beginning.
This is the story of National Gypsum’s contributions to the high-performance gypsum board used in commercial buildings and residential structures today.
What is high-performance construction, and how does gypsum board contribute to it?
The built environment is responsible for 40% of global greenhouse gas emissions. This includes building operations, construction and building material manufacturing. And because people spend an average of 90% of their time indoors, using high-performance building products can positively affect the productivity, health and well-being of the populace and the planet.
High-performance construction takes an integrated approach by reviewing systems from different perspectives, instead of approaching building components and systems separately. This means that while gypsum board is a key component in fire-rated walls, ceilings, floors and roofs, as a high-performance building product it can also provide benefits related to acoustics, indoor air quality, resilience and moisture resistance.
How a gypsum board innovation spurred the founding of National Gypsum
When National Gypsum entered the gypsum wallboard market in 1925, it did so with a new gypsum board formulation driven by the knowledge and experience of a man who was formerly employed at Beaver Products Company. Joe Haggerty, who was the first president of National Gypsum, had been experimenting with a new formula for gypsum board in his home kitchen, combining starch and ground-up newsprint to make it lighter and more flexible and help the face paper adhere. His work produced an early version of wallboard at the company’s first plant in Clarence Center, N.Y. Haggerty joined forces with others to create and market a new and improved gypsum wallboard.
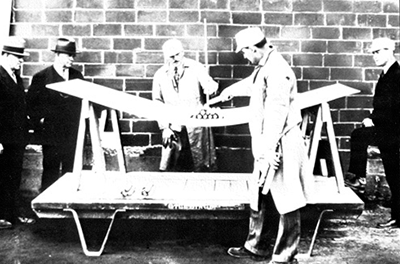
The goal was to create a superior product that would cost no more than other brands. They produced and scrapped a quarter million dollars’ worth of wallboard at their new plant before perfecting the product they would take to market.
Demonstrations were conducted to highlight the new board’s strength and flexibility by placing a board across two sawhorses and adding window sash weights in the middle until the board broke. They repeated the process with the competitor’s heavier board to show how the National Gypsum board’s superior qualities allowed it to hold significantly more weight before breaking.
XP drywall: Solving the construction industry’s mold problem
During the last quarter of the 20th century, new building codes and regulations aimed at improving energy standards resulted in significant changes for the construction industry.
Gone were the days of the “drafty” home, where airflow helped keep humidity at bay — albeit to the detriment of the structure’s energy efficiency. New buildings were instead designed to be airtight, using more insulation and a better sealed building envelope to help decrease the need for excess heating or cooling. And while this accomplished the goal of reducing energy waste, many of these new, well-sealed buildings began to experience an entirely new problem: indoor mold growth, often on the back of drywall panels and, subsequently, within the wall cavities.
For the drywall industry, the race was on to deliver a gypsum board that not only was moisture resistant but also inhibited mold and mildew growth.
Often, innovation is driven by inventive minds that can see what others don’t by connecting the dots between two disparate things. That’s how PURPLE XP® — a new mold- and mildew-resistant drywall with eXtra Protection against mold and moisture introduced in 2003 — came about: The product development team at National Gypsum decided to test SPORGARD®, an antimicrobial formulation created as a food preservative, to see if it could inhibit mold and mildew on drywall.
After extensive testing, the results were conclusive: It did, and did it well!
Soon, XP drywall — and its distinctive PURPLE, high-performance paper facing — was turning job sites PURPLE as the building industry adopted it as a preferred, cost-effective solution for interior walls.
But just as National Gypsum’s founders weren’t content to rest on a single success, the company’s product development team began to expand the PURPLE brand with new premium and specialty gypsum boards. This marked a wave of innovation at the company, as it developed and launched a growing line of high-performance drywall products designed to solve a wide range of building needs, including the following:
- PURPLE XP® Hi-Abuse® Drywall delivers enhanced protection against scratches and scuffs in high-traffic areas.
- PURPLE XP® Hi-Impact® Drywall provides additional protection in areas prone to cavity penetration.
- PURPLE SoundBreak® XP® Gypsum Board and SoundBreak XP Retrofit® Gypsum Board are engineered to reduce sound transfer.
PURPLE eXP: Delivering performance that gets the job done inside and out
With PURPLE drywall providing innovative solutions for indoor applications, National Gypsum tapped its moisture- and mold-resistance technology to create a new line of products that could reliably withstand extended exposure to the elements. The PURPLE eXP® line was introduced to the market as the solution for high-performance exterior building envelopes for wood- and metal-stud construction.
Featuring a technologically advanced fiberglass-faced gypsum panel, the eXP line was quickly hailed for its excellent weather and water resistance. And because it was dimensionally stable under changes in temperature, eXP also resisted warping, rippling and buckling, making it ideal for exterior conditions.
- Gold Bond® eXP® Sheathing is designed for use as a substrate for exterior cladding and comes with a 12-month exposure warranty, thanks to its specially designed PURPLE fiberglass mat facer on the front, back and sides.
- Gold Bond® eXP® Tile Backer Gypsum Panel has a specially formulated acrylic coating designed for use as a substrate for tile applications in high moisture rooms.
- Gold Bond® eXP® Interior Extreme® Gypsum Panel is a highly mold, mildew and moisture resistant gypsum board ideal for pre-rock applications.
- Gold Bond® eXP® Interior Extreme® AR Gypsum Panel has a denser core and an enhanced glass mat for increased resistance to indentation and abrasion.
- Gold Bond® eXP® Interior Extreme® IR Gypsum Panel is ideal for interior applications requiring increased resistance to incidental moisture and wall penetrations.
- Gold Bond® eXP® Shaftliner Gypsum Panel features a Type X core used in advanced fire-rated systems for cavity shaftwalls and area separation fire walls.
Innovation that goes beyond gypsum board
Following the success of PURPLE, National Gypsum’s push to develop and deliver innovative products that solve industry challenges became a core strategy for the company’s other affiliate brands as well. And, similar to the goals of the company’s founders back in 1925, product advancements for both PermaBASE® cement board products and ProForm® interior finishing products focused on improved performance and ease of installation.
PermaBASE: A versatile cement board that prevents water damage and reduces installation time
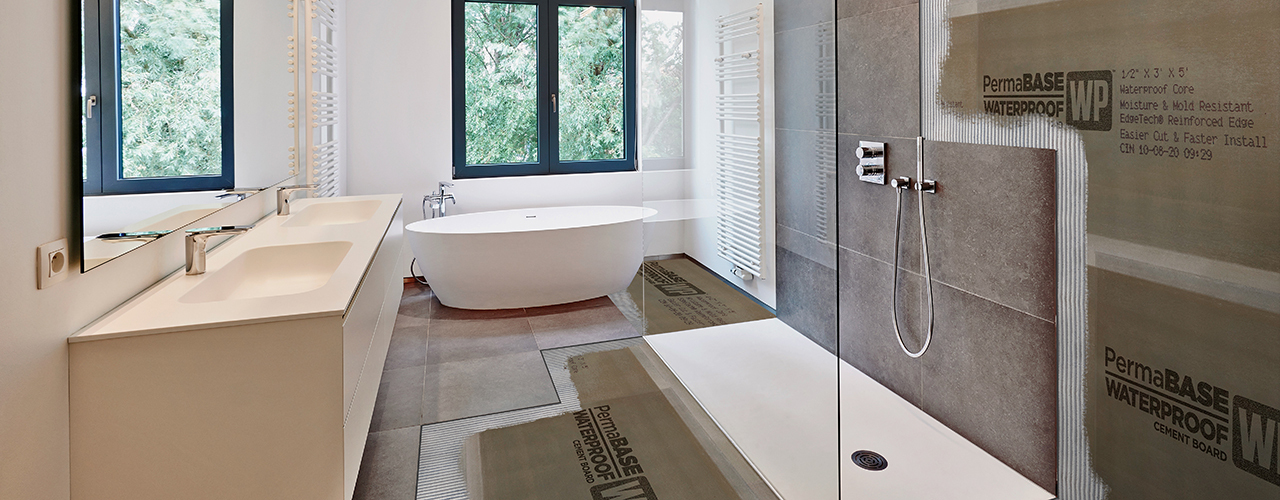
For years, PermaBASE® has offered the industry’s largest variety of cement board for both indoor and outdoor applications. Using lightweight polystyrene beads within the Portland cement core, PermaBASE products are also significantly lighter and easy to cut, while EdgeTech® technology allows fasteners to be installed closer to the edge without fracturing like other cement boards.
In 2020 the product development team began integrating a proprietary waterproofing ingredient during the PermaBASE manufacturing process. This, in turn, gave birth to a new version of its versatile cement board: PermaBASE WP® Waterproof Cement Board.
The new product quickly became known for its ability to help prevent harmful and costly water damage. This made PermaBASE WP ideally suited for interior wet areas, such as a shower enclosure. The board’s smooth surface made it an excellent substrate for tile and other decorative finishes, while the combination of cement and fiberglass mesh gave the board exceptional strength and durability.
Taking advantage of the product’s versatility, the next step in its evolution featured the addition of a layer of rigid insulation to create PermaBASE CI® Insulated Cement Board. By combining the strength and benefits of PermaBASE Cement Board with a high-density polyiso insulation, PermaBASE CI offered an ideal substrate for exterior thin brick and stucco finishes that also meets or exceeds most continuous insulation requirements.
ProForm: Low-dust, mold-/mildew-resistant joint compound that contributes to indoor air quality during and after construction

It doesn’t make sense to provide mold-, mildew- and moisture-resistant gypsum board if the joint compound used to finish it supports mold and mildew growth. That’s why joint compounds manufactured by ProForm Finishing Products, LLC include mold and mildew resistance.
In 2009, ProForm introduced a product that also solved the problem of dusty worksites with a joint compound that reduces the amount of airborne dust. This is especially important for renovations in buildings that can’t shut down during a renovation, such as hospitals and offices.
Proprietary Dust-Tech® technology — available in ProForm® All Purpose Joint Compound and ProForm Lite Blue® Joint Compound — reduces sanding dust by up to 60% by causing most airborne dust from sanding to drop to the floor instead of remaining in the air.
DEXcell: Covering the entire spectrum of commercial roofing applications
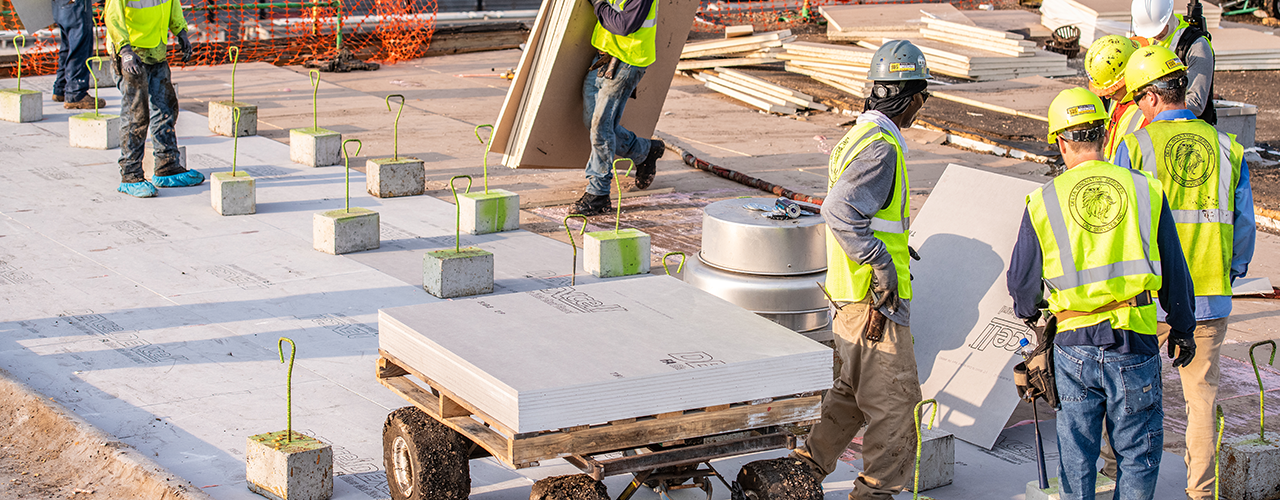
No matter the quality of the materials used to construct a commercial building, if the roofing doesn’t meet the same standards of performance it risks the integrity of the entire structure. The DEXcell® Roof Board product line was developed by National Gypsum to provide consultants, contractors and building owners with the best solution for a wide range of roofing applications.
All four DEXcell roof coverboard products provide weather and resiliency benefits, including improved wind uplift and fire resistance, while reducing outside sound transmission.
- DEXcell® Glass Mat Roof Board: Features coated fiberglass facers and enhanced mold-resistant gypsum core.
- DEXcell FA™ Glass Mat Roof Board: Includes heavy-duty, coated fiberglass facers and enhanced mold-resistant gypsum core.
- DEXcell® Cement Roof Board: Combines Portland cement and aggregate for a lightweight, and mold- and moisture-resistant panel with an exceptionally hard and durable surface.
For regions prone to hail storms, DEXcell FA VSH™ Glass Mat Roof Board boasts a stronger core designed to withstand a 2-inch ice ball traveling at 106 miles per hour.
Fostering a culture of innovation and service
True to its founders’ vision, National Gypsum Company continues to provide high-performance building products that solve problems. Whether it’s Gold Bond® gypsum board, ProForm® joint compound or PermaBASE® cement board, these product innovations contribute to resilient, sustainable buildings. In addition, storing, handling and installing the products is easier and more efficient for the dedicated tradespeople who construct the commercial buildings, multifamily structures and residential homes where we live, work and play.
Read the second blog in our three-part series to learn how National Gypsum pairs exceptional service with the high-performance products it provides.
The color Purple is a registered trademark of Gold Bond Building Products, LLC.
SPORGARD® is a registered trademark of LANXESS Deutschland GmbH, Germany.
National Gypsum Company is the exclusive service provider for products manufactured by Gold Bond Building Products, PermaBASE Building Products and ProForm Finishing Products.
Be the first to hear of new NGConnects blog posts by subscribing here for early access.
Related Blog Posts
Related Podcasts
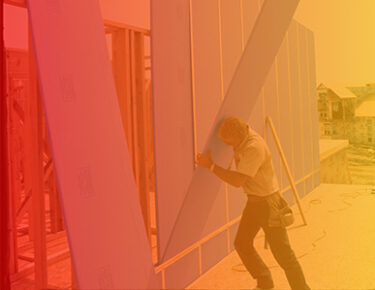
Episode 3: Key insights into area separation wall use and construction
From fireblocking and repairs to doors and plumbing, advance your...
Listen Now