
ProForm ready mix joint compounds: Time-tested, finisher approved
Explore these three tips to get the best out of every pail

Choosing the right drywall finishing materials — and using them to their peak performance — can shorten application times and reduce expenses related to callbacks and rework.
With more than a dozen options, ProForm Finishing Products, LLC, an affiliate of National Gypsum Company, has a ready mix joint compound suited to conceal and finish the full spectrum of drywall seams, corners and fastener heads.
As the ready mix name implies, these popular joint compounds are ready to use from the container. However, to get the best out of every pail, construction professionals must understand the impact of weather conditions on both product storage and usage, along with the importance of preventing mold and mildew growth before, during and after installation.
1. How environmental conditions affect ready mix drying times
Precautions should always be taken at the job site to minimize the adverse effects of weather on joint compound drying. Varying weather conditions can impact both the quality and appearance of taped drywall joints. For example, cool, wet weather will slow down the drying process, while hot, dry weather hastens the drying process. Exposure to winds, breezes or drafts while drying can also affect the performance of joint compounds.
The potential for finishing and decorating problems is minimized when temperature, humidity and airflow remain constant and as close to occupancy environmental conditions as possible. A minimum temperature of 50 F (10 C) should be maintained continuously for 48 hours prior to and throughout the finishing process until applied materials are thoroughly dry.
Ready mix joint compound drying times
Allowing sufficient drying times between coats of joint compound can feel like lost time on the job site, but patience is key. Typical problems from improper drying can include:
- Cracking: Deep fissures that form on the surface of the joint compound
- Excessive shrinkage: A noticeable reduction in the size of the joint compound as it dries, leading to gaps and uneven surfaces
- Ridging and beading: Raised ridges or beads that appear along the edges of dried joint compound
- Banding: Visible bands or lines on the surface of the joint compound, typically occurring when multiple layers dry at different rates
- Bond failure: Loss of adhesion between the joint compound and the underlying surface
Relative humidity, plus temperature, will affect the working characteristics of all joint compounds. The chart below is a helpful guide for determining approximate drying times for joint compounds under a variety of humidity/temperature conditions. (Note: The shaded area is below the minimum application temperature requirement of 50 F and is not recommended for the application of joint compound.)
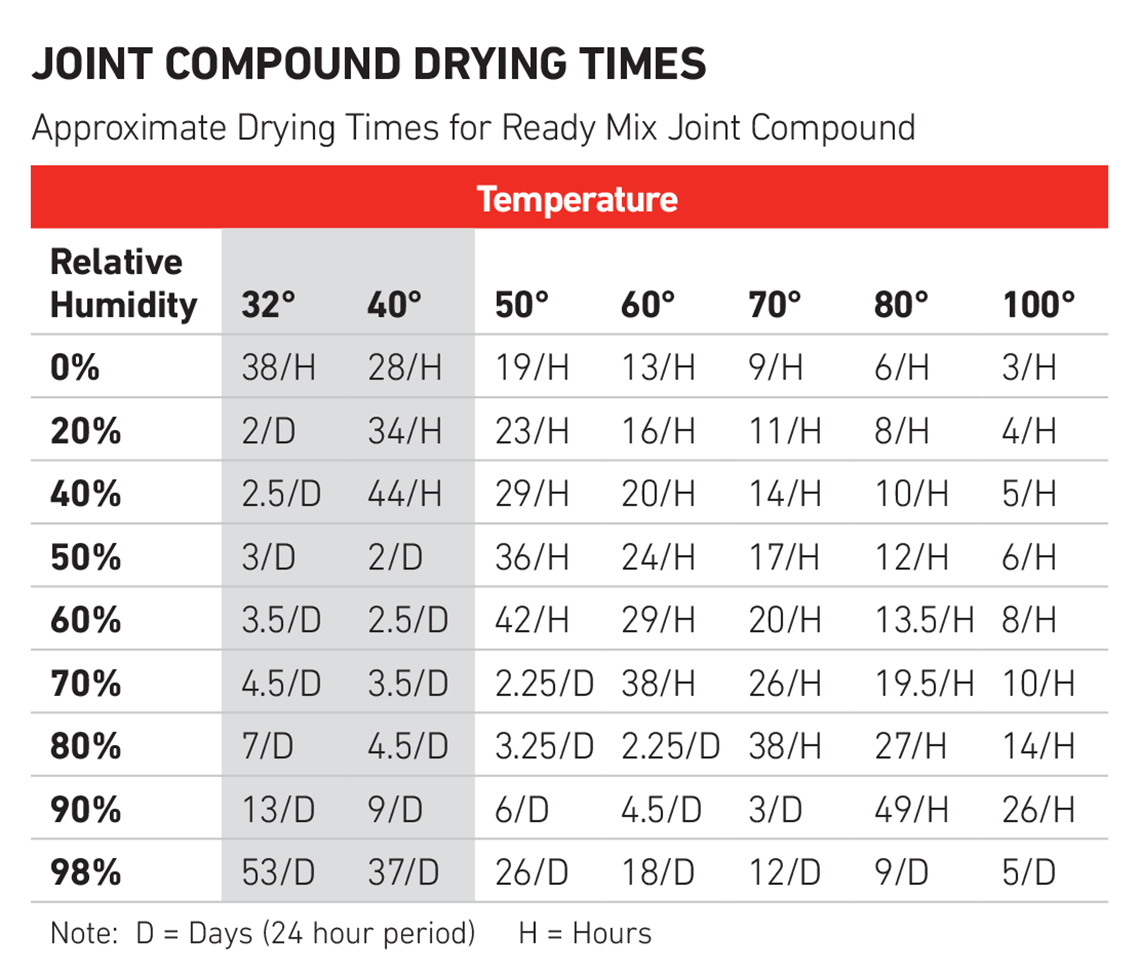
2. Best practices for storing ready mix joint compound
Under good storage conditions, which include never stacking more than two pallets of ready mix pails or cartons, the shelf life for ProForm ready mix compounds is up to nine months from the production date listed on the product packaging.
To prevent spoilage and freezing, maintain temperature at a minimum 50°F (10°C) and protect the joint compound container from exposure to extreme heat and direct sunlight.
If the ready mix is exposed to freezing temperatures, follow these steps:
- Allow the material to thaw at room temperature for at least 24 hours.
- Once thawed, turn the container upside down for at least 15 minutes.
- Turn the pail right side up, remove lid and immediately remix with an electric drill.
The joint compound should be lump-free and ready to use within one minute. However, if the product does not remix to a lump-free consistency, discard to avoid performance issues.
Once opened the shelf life of ready mix will depend on a number of factors, including proper storage conditions and securing the packaging such as making sure lids are secure and the provided plastic is covering the joint compound.
Pro Tip: To ensure the integrity of the drywall used with the joint compound, all wallboard delivered to a job site must be placed under cover immediately, be properly protected and not be exposed to outside elements such as rain, snow or other high-moisture conditions.
3. Preventing mold and mildew growth for ready mix
The ProForm family of ready mix joint compounds offers high-quality, consistent formulas that are also mold and mildew resistant. However, as with any building material, avoiding water exposure during handling, storage and installation of the joint compound — and after installation is complete — is the best way to avoid the formation of mold or mildew.
If a finished wall or ceiling gets wet from any moisture source, that source must first be identified and corrected. If mold or mildew growth occurs, or if you suspect it might occur due to environmental conditions and moisture, determine whether to attempt to dry and clean the affected areas or to replace the affected materials.
Care must be taken in this evaluation, and if you do not have the training or experience to recognize and make proper decisions about repair or removal, consult a mold remediation expert.
How ProForm Dust-Tech products deliver superior mold resistance
While all ProForm products offer mold and mildew resistance, ProForm Dust-Tech® products achieve the highest test scores. These products — ProForm® All Purpose with Dust-Tech® Joint Compound and ProForm® Lite Blue® with Dust-Tech® Joint Compound — were designed to provide extra protection against mold and mildew compared to standard ready mix compounds.
When used in conjunction with good design, handling and construction practices, ProForm Dust-Tech products can provide proven mold resistance.
- When tested by an independent lab per ASTM D3273, Standard Test Method for Resistance to Growth of Mold on the Surface of Interior Coatings in an Environmental Chamber, ProForm Ready Mix with Dust-Tech achieved a score of 10, the best possible score for this test.
- These products also resist the growth of mold per ASTM G21, Standard Practice for Determining Resistance of Synthetic Polymeric Materials to Fungi, with a score of 0, the best possible score.
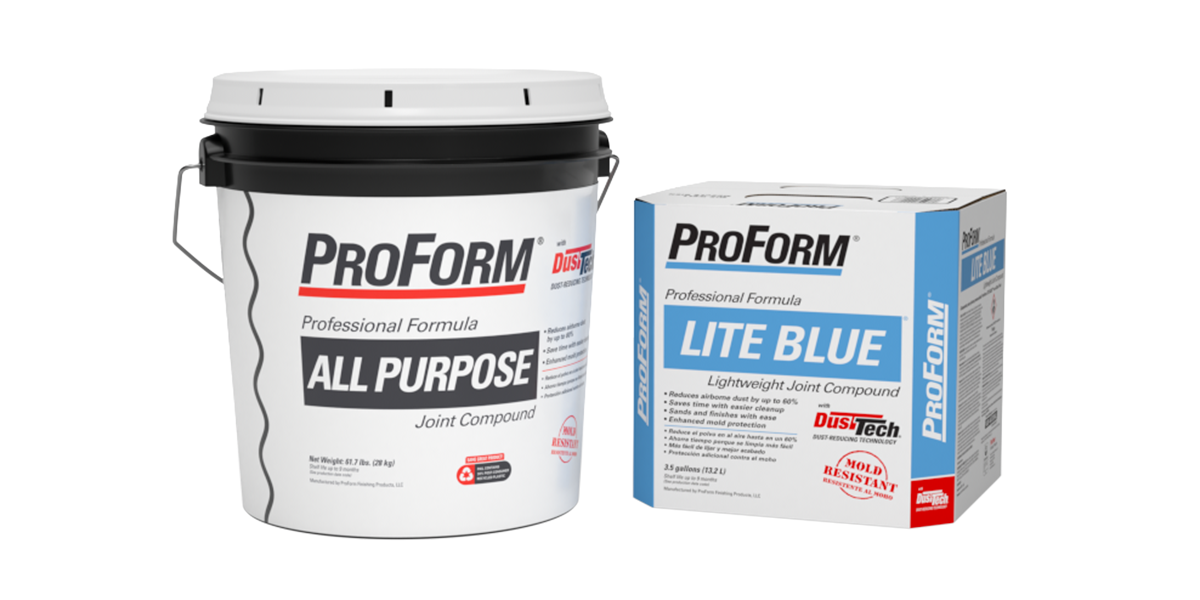
What about setting compounds?
To ensure best results, ProForm ready mix joint compounds should be used throughout a construction project. Factors such as the size of the project and tight timelines, however, can require choosing between ProForm ready mix and ProForm setting compounds. Setting compounds harden at set times ranging from five minutes to 210 minutes, which allows you to apply a second coat sooner than you could with ready mix.
To help you choose the best solution for your project, download the ProForm Finishing Products Construction Guide. The guide details the entire family of ProForm products, from ready mix and setting joint compounds to joint tape and texture products, along with more installation and troubleshooting tips.
ProForm Quick Set Lite™ Setting Compound
ProForm Quick Set Lite comes in a range of setting times — 5, 20, 45, 90 and 210 minutes — and provides a consistent spread for the entire time listed on the bag. Discover how to achieve the perfect setting mix, the difference between working time and setting time, and other helpful tips. Read More.
Be the first to hear of new NGConnects blog posts by subscribing here for early access.
Related Blog Posts
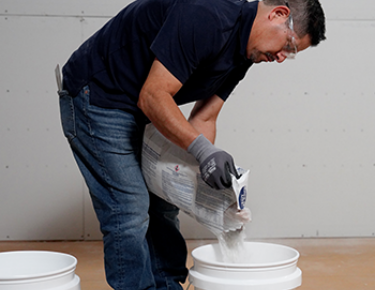
Master the mix: 3 tips for perfecting your setting compound
Maximize jobsite efficiency with ProForm setting compounds
Read MoreRelated Podcasts
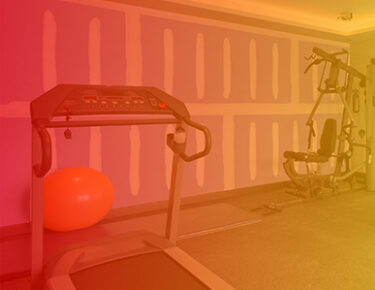
Episode 6: Understanding abuse- vs. impact-resistant gypsum board
Learn how these durable boards are constructed, tested and specif...
Listen Now